Table of Contents
Paper is a ubiquitous material that we use in our daily lives, from writing to packaging, and much more. But have you ever wondered how paper is made? In this comprehensive guide, we will take you through the process of how paper is made, from raw materials to finished product.
Introduction: The Importance of Paper
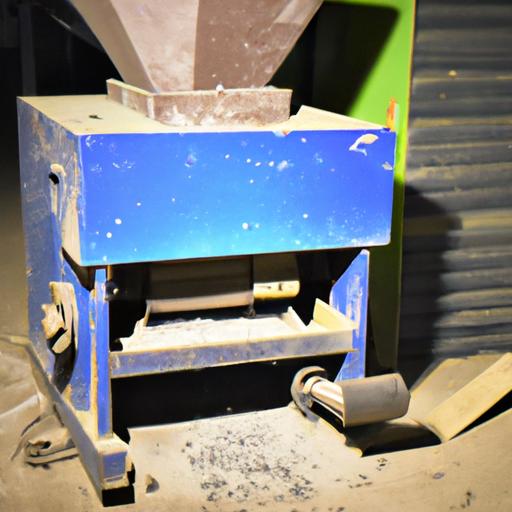
Paper is a thin material that is made from fibers, typically derived from wood pulp. The importance of paper cannot be overstated as it is used in various industries, including education, publishing, packaging, and many more. With the rise of digital media, paper consumption has decreased, but paper is still essential in many aspects of our lives.
Raw Materials for Making Paper
The raw materials for making paper are primarily fibers. These fibers can be derived from various sources, including:
- Wood pulp: The most common raw material for making paper is wood pulp, which can be obtained from softwood or hardwood trees.
- Agricultural residues: Certain agricultural residues, such as straw and bagasse, can also be used to make paper.
- Recycled paper: Recycled paper can be used to make new paper products, reducing the need for virgin fibers.
The process of obtaining these fibers varies depending on the source. For example, wood pulp is obtained through a process of chipping and pulping, while recycled paper is collected, sorted, and processed to remove any contaminants.
In the next section, we will discuss the pulping process in more detail.
Pulping
Definition of Pulping
Pulping is the process of breaking down raw materials into fibers that can be used to make paper. The process involves separating the fibers from the rest of the material, such as bark or leaves, and breaking them down into a pulp.
Types of Pulping
There are two main types of pulping: chemical pulping and mechanical pulping.
Chemical Pulping
Chemical pulping involves using chemicals to break down the raw materials into pulp. The two most common types of chemical pulping are kraft pulping and sulfite pulping.
Kraft pulping is the most common type of chemical pulping and involves using an alkaline solution, typically sodium hydroxide and sodium sulfide, to break down the lignin in the wood fibers. The resulting pulp is strong and can be used to make a variety of paper products.
Sulfite pulping involves using sulfurous acid to break down the lignin in the wood fibers. Sulfite pulping results in a softer pulp that is typically used for making tissue paper and other delicate paper products.
Mechanical Pulping
Mechanical pulping involves using mechanical processes to break down the raw materials into pulp. The two most common types of mechanical pulping are groundwood pulping and refiner mechanical pulping.
Groundwood pulping involves grinding the raw materials against a rotating stone to break them down into pulp. Refiner mechanical pulping involves using a refining machine to grind the raw materials into pulp.
In the next section, we will discuss the cleaning and screening process in more detail.
Pulping
Process of Pulping
Once the raw materials have been obtained, they are sent through the pulping process. The process starts with the raw materials being chopped and broken down into small pieces. The pieces are then mixed with water and chemicals, depending on the type of pulping being used.
In chemical pulping, the raw materials are cooked in a digester, which breaks down the lignin and separates the fibers from the other materials. The resulting pulp is washed and screened to remove any impurities.
In mechanical pulping, the raw materials are ground or refined to break down the fibers. The resulting pulp is then screened to remove any impurities.
Cleaning and Screening
Purpose of Cleaning and Screening
After the pulping process, the pulp is sent through a cleaning and screening process. The purpose of this process is to remove any impurities and to ensure that the pulp is of high quality.
Types of Cleaning and Screening
There are several types of cleaning and screening processes that can be used, including:
Centrifugal Cleaning
Centrifugal cleaning involves using a centrifuge to separate the pulp from any impurities. The pulp is spun at a high speed, causing the impurities to be thrown outwards while the pulp stays in the center.
Floatation Cleaning
Floatation cleaning involves using air bubbles to separate the pulp from any impurities. The pulp is mixed with water and air bubbles, causing the impurities to rise to the surface, where they can be skimmed off.
Screening
Screening involves passing the pulp through a series of screens to remove any large impurities. The screens are typically made of mesh and can vary in size depending on the desired level of purity.
Process of Cleaning and Screening
The cleaning and screening process typically involves a combination of these methods. The pulp is first sent through a series of centrifuges or floatation tanks to remove any large impurities. The pulp is then passed through screens to remove any smaller impurities.
After the cleaning and screening process, the pulp is ready to be used to make paper.
In the next section, we will discuss the papermaking process in more detail.
Papermaking
Definition of Papermaking
Papermaking is the process of turning pulp into paper. The pulp is diluted with water and then fed onto a paper machine, where it is formed into sheets and dried.
Types of Papermaking
There are two main types of papermaking: machine-made paper and handmade paper.
Machine-Made Paper
Machine-made paper is the most common type of paper and is produced on a large scale using paper machines. The process involves feeding the pulp onto a paper machine, where it is formed into sheets and then dried. Machine-made paper is typically used for everyday items such as printing paper, newspapers, and packaging materials.
Handmade Paper
Handmade paper is produced on a smaller scale and is made using traditional papermaking methods. The process involves beating the pulp by hand and then forming it into sheets using a mold and deckle. Handmade paper is typically used for specialty items such as stationery, fine art, and bookbinding.
Process of Papermaking
The process of papermaking involves several steps, including:
-
Forming: The pulp is diluted with water and then fed onto a paper machine, where it is formed into sheets.
-
Pressing: The sheets are then pressed to remove any excess water and to make the paper more uniform.
-
Drying: The sheets are dried using heat and pressure, typically on a large drying cylinder.
-
Sizing: The paper is treated with sizing agents, such as starch or gelatin, to make it more resistant to water and ink.
-
Calendering: The paper is then passed through a series of rollers to make it smoother and more consistent in thickness.
In the next section, we will discuss the finishing process in more detail.
Finishing
Definition of Finishing
Finishing is the process of treating the paper after it has been made to improve its properties or appearance. The finishing process can include coating, cutting, folding, and other treatments.
Types of Finishing
There are several types of finishing, including:
Coating
Coating involves applying a thin layer of material, such as clay or latex, to the surface of the paper to improve its properties, such as printability or water resistance.
Cutting
Cutting involves cutting the paper into the desired size or shape using a cutting machine.
Folding
Folding involves bending the paper to create folds or creases, typically using a folding machine.
Embossing
Embossing involves pressing a design or pattern onto the surface of the paper to create a raised or indented effect.
Process of Finishing
The process of finishing can vary depending on the type of finishing being performed. For example, coating involves applying a thin layer of material to the surface of the paper using a coating machine. Cutting involves feeding the paper into a cutting machine and cutting it into the desired size or shape.
In conclusion, the process of making paper involves several steps, including obtaining the raw materials, pulping, cleaning and screening, papermaking, and finishing. Each step is crucial in creating high-quality paper that can be used in various industries. Understanding the papermaking process can help us appreciate the importance of this ubiquitous material in our daily lives.